Romy the Cat wrote: | Jorge, your comment about
the physical instability of the pipe stack is well taken. I think if it is gone
from metal then it is possible to make it steady. In the way how Antony want to
do the pipe feet I think it might be possible to run guy wire to the top of the
pipes hip and to anchor them this way. I am sure the people who are good with industrial
design in metal can come up with some solution, it was never my objective to
think about it deeper. For sure the design need to be safe and to be more or
less portable. It is not the last factor is that it has to be earthquake proved.
It sounds ridicules but you do not want to have a minor earthquake and to find
your speakers flying to the floor and crash your amps and tonearms.
|
|
In my 43 years of life living only in this part of the world I have never felt the ground shake apart from when a neighbour was geligniting tree stumps out of the ground when I was a kid. That looked so much fun but I was never allowed to join in!
But I do take your point Romy, and to be honest, based on what my experiments have yielded thus far and where I expect the cannon stacks to be placed in the room in the event of an earquake I think they would tilt into the wall and probably crush some gyprock, but I doubt they would bend or topple.
Below are a couple of images from where I have loosely stacked some cannons to try to gauge if the stack was going to be rigid enough...
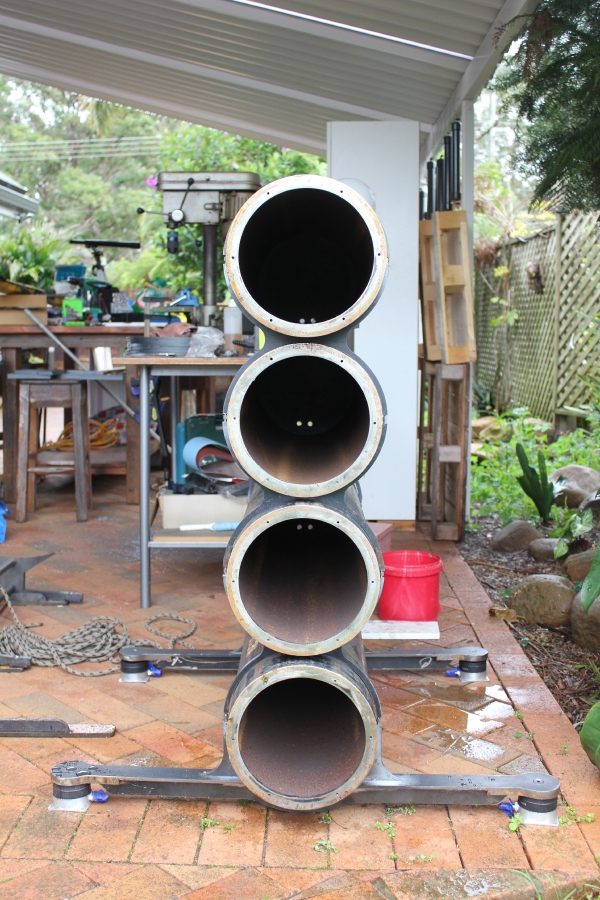
At 4 cannons high and with only two sets of braces (each without their gaskets) this cannon stack was rock solid. The braces are 10mm x 10mm steel with M6 double ended screws to bind them together. Of course as I go higher the situation may change, but I can stop at 6 or 7 or 8 with this design if I have to.
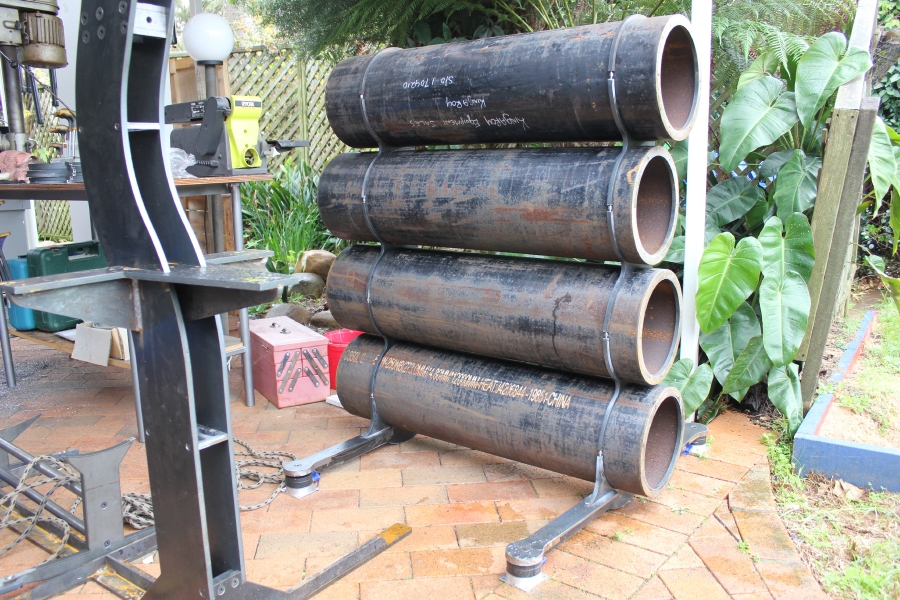
After powdercoating I have experimented with the amount of ringing in the pipes and what level of damping I require. Below you see one tube with four sets of bracing applied, this time with the 2mm cork gaskets installed. The braces work as a 'pre-tensioning' device in that they apply considerable pressure to the tube which further increases the rigidity of the pipe walls. Adding the third brace really knocked the amplitude out of the excitements and decreased the duration of ringing and the fourth brace further improved the result. However, there was still some residual energy being released as ringing, quite low in amplitude, but still there. With four braces applied to the 4.8mm wall steel pipe, I would rate a knuckle wrap as the equivalent of doing the same on a 16mm plate of steel. I researched damping paints as well as automotive butyl rubber/aluminium CLD sheets and have ordered some of the latter to place inside the pipes to eliminate the last of the stored energy. Driver excursions as going to be quite small if I can get 6 or 8 tubes in a stack so I actually have high hopes that I can make these steel enclosures very inert for their purpose.
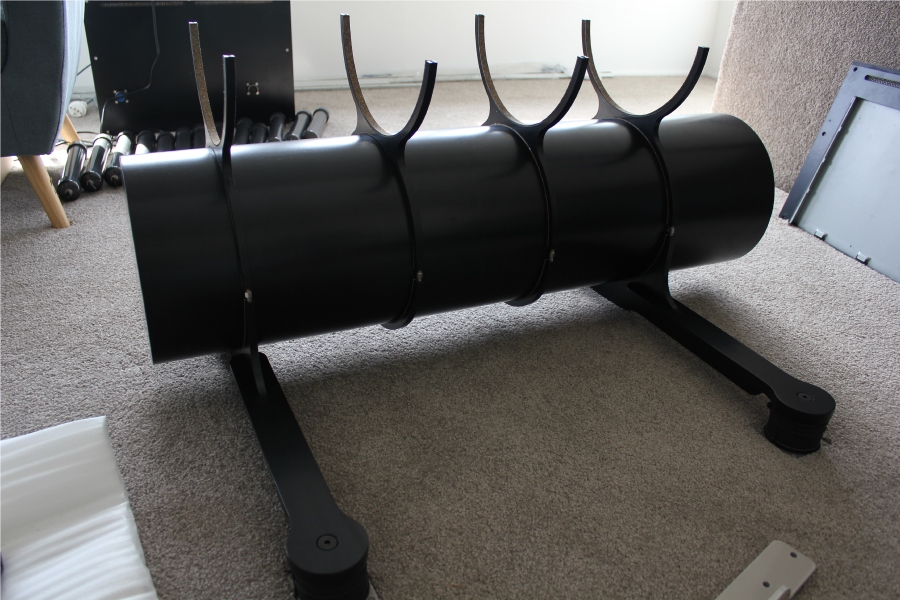
Romy the Cat wrote: | I never was a huge fun of the pipe design that you and Anthony looks like embrace. There is none contestable topological advantage that the pipes might be aligned in a curve to make a very perfect time alignment. This is given. How practical it is I do not know. I think it need to be aligned one pipe a time, starting from the bottom during the pile assembly… Another point is the sharp rollback from the back wall. The pipe design will have a permanent sharp enclosure mode deriving from the one single reflection surface. The pipe des has it as well but there are many reflection surfaces and the modes are kind of defused. With the pipe I think the reflection mode should be only one and it should be more prominent than with box. Saying all of it and understanding that you have good 2 inch foam in the box, or perhaps 4” in the back wall, not to mention that you guys run it all at very LF it is possible as well then my comment about reflection mode are purely theoretical and will be negligible in practice. I never experiment with pipes and do not know what work in them and what is not.
|
|
I will be experimenting with stuffing the pipes. At this early stage, I want to first see if I can make the enclosure inert and then move on to acoustic testing.
Romy the Cat wrote: | If I were building my system again from scratch and would follow the same topology then I would probably go with stackable individual rectangular boxes with one or with two driver, probably one. The construction of the sealed boxes is VERY not expensive and if you order them in bulk then you get a large discount. But it is me and I do not particularly fide the pipes being more attractive visibly. Also, I am not sure how metal enclosure would work for damping. For sure my opinion shall means very little for those who desisted to use pipes and I am sure that it to make the use the pipes as an objective and took this task seriously then it is possible to make the pipes to work out well… |
|
At this stage I am not wedded to the pipes idea, but am wedded to the idea of a modular bass stack whether that be one or two drivers per box, steel or wood or some other material.
|