Posted by Paul S on
07-02-2013
|
fiogf49gjkf0d N-set, have you tried wall mounting for the TT suppport? This can improve on floor borne solutions in typically framed structures. Perhaps you know the sizes and spans of the floor joists and have it all worked out already. Otherwise, as a generic observation, weighting the supended floor joists does not add up very fast as far as resonant frequency is concerned, and structural overload should be avoided (for obvious reasons). Whenever possible, the best way to tune floor joists is shoring, which is well covered in the Romy's New Listening Room thread (I think...).
Best regards, Paul S
|
|
|
Posted by N-set on
07-02-2013
|
fiogf49gjkf0d Paul, I thought about the wall mount, but eventually decided to go with a more universal, pref. end of life solution, I could place anywhere. I've never had a dedidcated rack, a time to have one. The result is a slate-on-steel-frame 500kg mastodont, I'm about to finish (will post the resluts soon in a separate thread, here is a work in progress diary: http://www.lencoheaven.net/forum/index.php?topic=11724.0 ). The idea is to have a massive structure supporting large (1,4mx0.7m) Vibraplane-style pneumatic decoupled plane for TT's/CD's/RIAA etc. The mass is there not so much to lower the res. freq. of the floor (with TT it's never low enough), but rather to make the vibration amplitude smaller. This is what they do in optical tables. Yes, i'm quite concerned with the structural load, let's hope it'll be ok. The geometry of my floor I do not know, I did not make it. Actually, this is a decorative suspended wooden floor on top of a armed concrete/brick (if I'm right) building structure. It's not only wood.
Cheers, N-set
|
|
|
Posted by Paul S on
07-02-2013
|
fiogf49gjkf0d N-set, of course the finish flooring is supported by some sort of structural "members". These MIGHT be reinforced concrete, and so MIGHT be quite strong, depending on the whims of the builders at the time of construction, and considering any loss of strength and/or elasticity over time. If the floor structure is wood joists, or if it is "engineered" joists, then you might want to ease into loading 500kg out into the span! Remember that part of the problem with amplitude that you wish to diminish results from a design load that is within the member's acceptable load range, based on its modulus of elasticity!
Best regards, Paul S
|
|
|
Posted by N-set on
07-02-2013
|
fiogf49gjkf0d Paul, wood it is not almost for sure: there was hardly any wood and wood craftsmen available in Gdansk in the 50's when my building was built. Almost completely (95%) destroyed in march 1945 when pushing the Germans out, it was rebuit mostly using reinforced concrete-a very peculiar solution, I've been told a local Gdansk invention. My roof for example is 100% reinforced concrete, not a single wooden member, I've never seen anything like that. The question is how precisely the floor is constructed and how strong it is after 60yrs. The good thing is that the rack will be closely between two chimneys, so I hope the floor is additionaly reinforced there.
Cheers, N-set
|
|
|
Posted by Paul S on
07-02-2013
|
fiogf49gjkf0d N-set, I've seen and done plenty of all-concrete construction, including floors and entire roof structures, standard, pre- and post-tensioned, and also shot-crete. Ironically, concrete itself actually gets stronger over time, for many, many years (more than 60). Although the iron reinforcement does not get stronger, it usually holds up OK, except in salty air or in salt spray, or where it was not sized, spaced, lapped, routed, and/or covered properly to begin with. So, no surprise, it gets down to exactly how it was implemented. In extreme economic/political conditions, some 3rd world concrete construction is nowhere near as strong as typical US post and beam with truss joists (eg., the World Trade Center...), and some would take the weight of a helicopter landing on it. To absorb a gratuitous 500 kg out in a span, let's hope your building is (somehow...) the latter type. Whether "between the chimneys" would help depends on exactly how they did it. If the floor structure is "headed"/cut out around the chimneys, it does not help, unless the chimneys are solid masonry and the racks could be fastened directly to the chimneys, as well as the wall behind them. It also helps if the rack is right up aginst a full bearing wall, since it would then extend as little as possible into the floor span.
Best regards, Paul S
|
|
|
Posted by N-set on
07-02-2013
|
fiogf49gjkf0d I will upload some pictures and more details when the rack is at my place in few days and pre-assembled in it's "version 1". In the meantime, for those with masochistic tendencies, here is a diary of my ignorance on the subject:
http://www.lencoheaven.net/forum/index.php?topic=11724.0
Thanks! N-set
|
|
|
Posted by N-set on
07-04-2013
|
fiogf49gjkf0d Paul S wrote: | N-set, I've seen and done plenty of all-concrete construction, including floors and entire roof structures, standard, pre- and post-tensioned, and also shot-crete. Ironically, concrete itself actually gets stronger over time, for many, many years (more than 60). Although the iron reinforcement does not get stronger, it usually holds up OK, except in salty air or in salt spray, or where it was not sized, spaced, lapped, routed, and/or covered properly to begin with. So, no surprise, it gets down to exactly how it was implemented. In extreme economic/political conditions, some 3rd world concrete construction is nowhere near as strong as typical US post and beam with truss joists (eg., the World Trade Center...), and some would take the weight of a helicopter landing on it. To absorb a gratuitous 500 kg out in a span, let's hope your building is (somehow...) the latter type. Whether "between the chimneys" would help depends on exactly how they did it. If the floor structure is "headed"/cut out around the chimneys, it does not help, unless the chimneys are solid masonry and the racks could be fastened directly to the chimneys, as well as the wall behind them. It also helps if the rack is right up aginst a full bearing wall, since it would then extend as little as possible into the floor span.
|
|
Paul, I've investigated my building a bit. The comparison of the post-WWII Eastern Europe and the (I hate this expression) "3rd world", as you put it, is probably quite adequate, but there is one important difference: they really had nuclear blasts in mind when it comes to buildings from the 50's era! All the bearing walls (exterior and interior) are 38cm solid masonry (possibly aditionally reinforced?). My floor is actually the last level before the roof so it carries all the weight of the heavy, concrete slanted roof (through very elegant reinforced concrete supports) and whatever tons of wet snow happen to be on it. It's supported from below by extra steel/concrete beams as well as a net of inner bearing walls (my floor sits on top of them). The 500+kg monster will be in the span unfortunately, but right to the solid masonry chimney channel, incorporated in an inner bearing wall, and some 1-1.5m from one of the support steel beam on the other side. I think the additional 500kg on a sq. meter should be ok under such conditions. Tomorrow will show...
Cheers, N-set
|
|
|
Posted by de charlus on
07-05-2013
|
fiogf49gjkf0d Sounds interesting - any pictures yet? Secondly, are you roughly aware of the cost of the exercise, and are you satisfied with the results?
de Charlus
|
|
|
Posted by N-set on
07-05-2013
|
fiogf49gjkf0d de Charlus, the rack is still not at my place after the rework (it turned out to shake like a gelly fish--I refer everybody interested to the lencoheaven thread). I'll post pictures and some details when it's here and the slate is on it's place. Cost? Even including the rework, since it's Poland and I'm smart with finding craftsmen is probably of the order of what you'd pay for a nice dinner for two in a fashionable restaurant, incl. a good tip. Satisfied--too early to talk about it. There is a second phase planned after I get the basic structre: adding pneumatic isolators and all the acompanying structure (damping reservoirs, manometers, pneumatic switches, etc). It'll all take some time though.
Cheers, N-set
|
|
|
Posted by N-set on
07-25-2013
|
fiogf49gjkf0d So here is the promissed picture of yet unfinished rack:
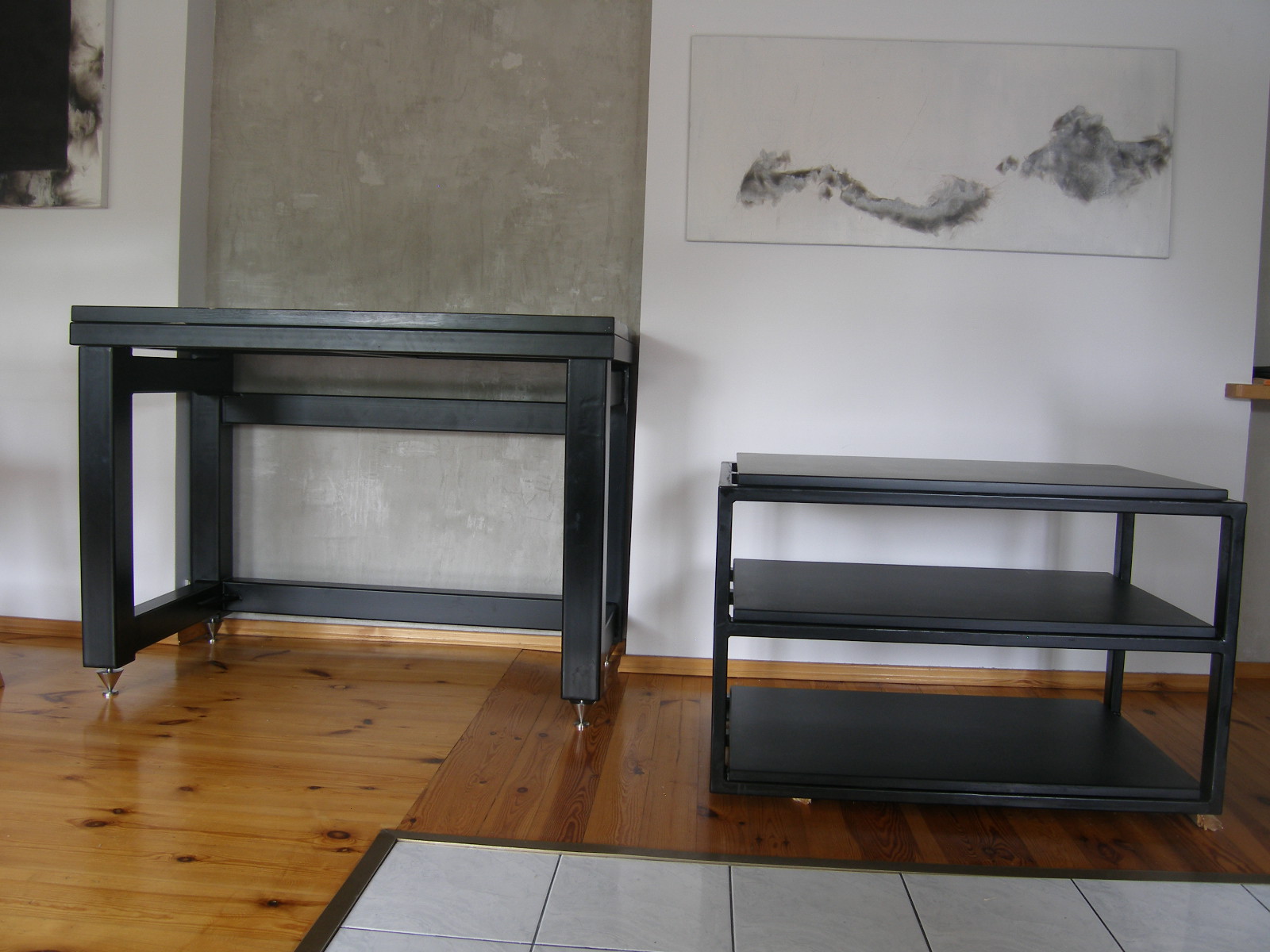
It's huge (the columns are 10x10cm) but still quite elegant-looking in my room. The electronics rack on the right will be put inside the TT rack when I finish working on it. It's all thick (4-5mm) steel profiles, sand+shots and perlite (much better!) filled and the best is the stone: italian volcanic slate, marinated in vaginal liquids of Baltic virgins and rubbed with their brests. The picture does not even come close to the rich, deep graphite tone it has!
The ridigity with all hiting and taping tests is OK. This is v2 actually, the 1st version was a copy of RixRax Hoodoo but was not rigid enough, hence I cut the inner cage out...respect to RixRax if they managed to make it all rigid!. But anyway I'm keep being surprised how elastic steel is! It's definitely not vibration free and hiting the racks with a hand create low freq. vibrations...I'd probably have to pour it out of concrete to have it dead. The floor did not collapse so far, moreover the 300+kg TT stand is quite easy to slide. Phase 2 of the project is adding pneumatic suspension below the upper TT table (the steel frame and the 4.5cm thick slate on top of the columns) and probably under the electronics cage. This should create a big 140cmx70cm vibraplane for the TT. I also plan to interface slate to steel using 3mm sorbothane strips and to modify the spikes a la RixRax.
Cheers, N-ste
|
|
|
Posted by de charlus on
07-25-2013
|
fiogf49gjkf0d Actually, those look pretty damn good; elegant, as you say. Let us hope that they live up to the promise of their appearance, and all will be well.
Cheers
de Charlus
|
|
|
Posted by N-set on
07-25-2013
|
fiogf49gjkf0d Thanks de Charlus. Indeed countless hours with CAD soft and redoing the thing did produce a nice visual effect (my pic is quite shitty and deformed...sorry). How it will behave? Time will show. Listening to audio racks is one of the last things on earth I'd like to do, it's main role is to isolate from the wooden floor vibrations, without adding own vibrations. This last condition turned out to be very very complicated for me, as I have chosen an inelegant, brurte force high mass approach.
Cheers, N-set
|
|
|
Posted by Paul S on
07-25-2013
|
fiogf49gjkf0d Beautiful racks, N-set! They actually look like grown-up versions of my Target racks. Are you amazed that they yet vibrate when struck? God only knows what it takes to become totally inert, and - of course - eventually - everything moves at some "frequency". Naturally you will tune the TT out of hysteresis territory, one way or the other. Something to be mindful of is if/how any machinery (like air conditioning or elevators, etc.) or adjacent doors closing may affect the shelves and/or the objects on them. A friend in a "loft" (an old warehouse redux) had ridiculous LF/ULF resonances from all manner of sources he never saw coming until they happened. From your earlier descriptions this sounds unlikely in your case. FWIW, I never noticed any audible effects from the "native resonance" of my Target stands. You might find it best to somehow "decouple" the racks from the wood floor if the latter has its own vibratory issues. While wood (like the floor) tends to exhibit a rather broad spectrum, the racks (if they do anything at all) are more likely to amplify a (relatively) narrower band.
Best regards, Paul S
|
|
|
Posted by N-set on
07-25-2013
|
fiogf49gjkf0d Paul, thanks! I'm quite happy to hear I'm not the only one fighting vibrations in a seemingly dead structures...It takes a lot of thinking to properly isolate and damp vibrations. Not unlike in the complementary problem: reproduction of the audio range. Just like in the latter there is no universal device capable of reproducing the whole spectrum equally well, here too there is no one single element or even a strategy decoupling all 6 vibrational axes in the all interesting freq. Here is my big mistake---the 1st version of the rack:
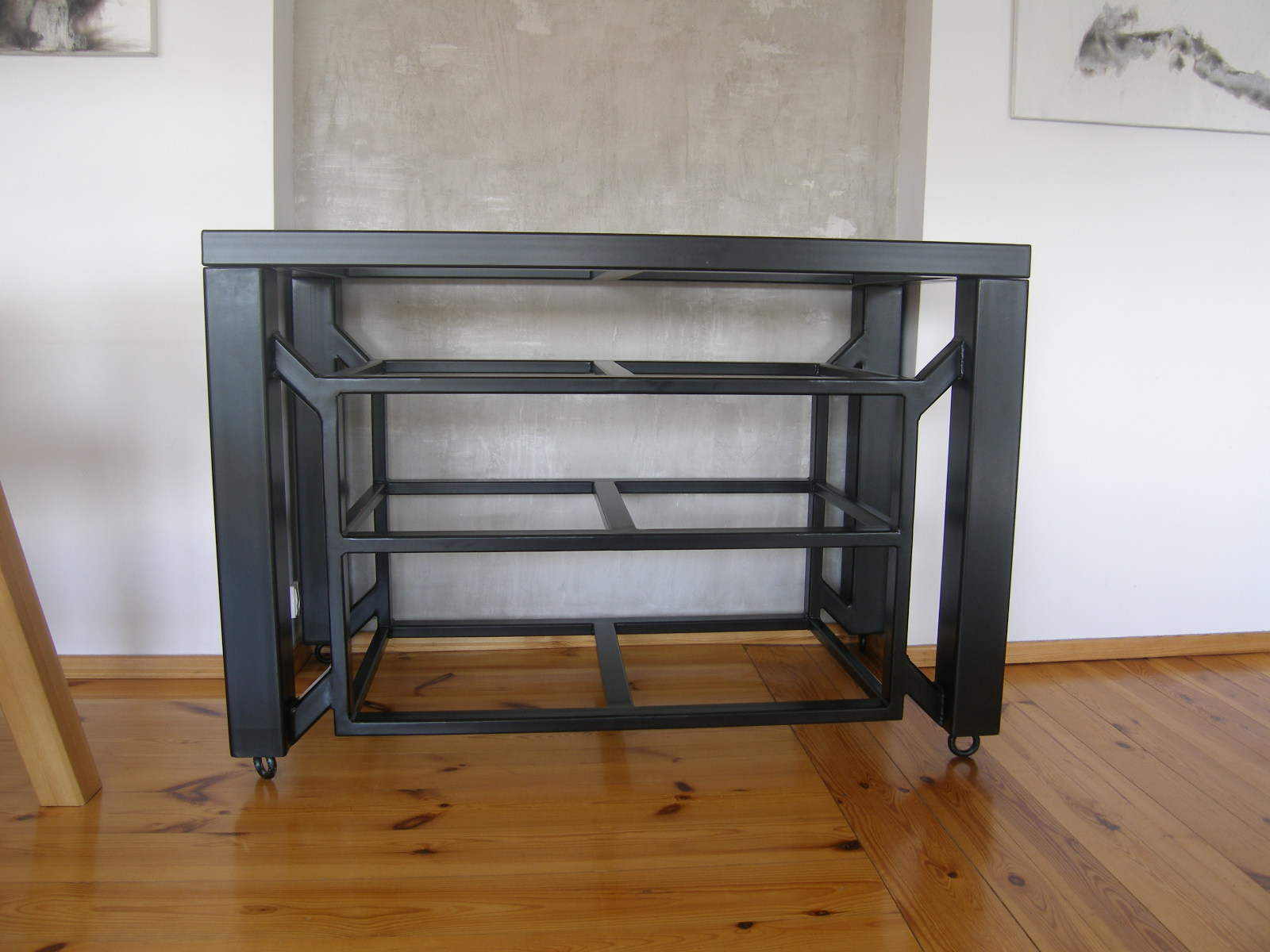
The inspiration is obvious--RixRax Hoodoo. My poor imitation shaked like a gelly even with a gentle touch! I suspect the inner, sand loaded cage acted like a big mass, suspended on 4 springs (diagonal members) terminated at the columns. This has been a big lecture for me: stupid, indiscriminative mass loading is a road to nowhere. It lowers fres., alright, butt it also lowers damping! How could I, a phisicist by profession, have overlooked that!? What I got was a gelly, shaking at some few Hz, I guess perfectly in the 3-5Hz resonant range of the pneumatics I plan to use. So instead of giving the pneumatics (my main ULF decoupling element) a solid base to work against, it would inject it's own vibration. That's why I've cut the inner cage out and bound the columns with 10x8cm 4mm thick, perlite (lighter than sand!) loaded profiles. Adding stiff members greatly increased rigidity, controllig mass keept fres. and damping high enough to be (hopefully, I haven't measured that) comfortable for the pneumatics. It all still shakes as a whole at ~1-2Hz when strongly hit, which I attribute to the spikes (create inverted pendulum with a high mass on top...fucking spikes).
Decoupling from the floor: electronics cage I plan to put on the pneumatic suspension. The TT table will have the neumatics on top of the columns. To the floor it's interfaced with spikes...I just could not workout a better solution now, giving a nice leveling feature on uneven surfaces. If I manage to fish a second 4.5cm thick slate slab, I'll put it below the rack and probably change the spikes to my own idea of rotary bearings.
Cheers, N-set
|
|
|
Posted by Paul S on
07-25-2013
|
fiogf49gjkf0d Here is an idea from Walker Audio that actually makes some sense in some cases:
http://walkeraudio.com/?product=valid-points-resonance-control-kit
To be sure you understand, I am NOT suggesting you spend anywhere near 625USD for something like this. Rather, take a look and DIY, to suit.
I did not bother to check this time, but the brass "pucks" used to be filled with Pb, and one might use that "super-condensed" felt between the puck and the wood floor.
No, this does not (much) change the "pendulum effect". However that might be addressed by simply attaching the rack to the walls, perhaps with something "pneumatic". Obviously, anything short of "no movement" not only reduces amplitude, but in this case it also (likely) raises the resonant frequency, because it "shortens the arc". Depending on the original source/impetus for the movement, shortening the arc to the "right length" might actually effectively dampen it considerably via "feedback". Of course, this pendulum cuts both ways, and augmentation is also theoretically possible. But what the hell, you have to actually, physically try any solution, in any case.
Best regards, Paul S
|
|
|
Posted by Romy the Cat on
07-25-2013
|
fiogf49gjkf0d A very nice made rack. I do not know if “stupid, indiscriminative mass loading is a road to nowhere”. To me all of the solutions with rack design are road to nowhere. There are many reasons why some of the solutions are better or worse and they all do make since but I still need to see if and how the actually affect sound of playback. I spent long houses experimenting with all imaginable suspension and decouples, using a good stethoscope to hear how vibration are propagated but I was not able to find how better noise in stethoscope impact the sound of the components. I might say that I can hear some difference with different racks but I would not definitively say that one solution is better then another. Even more: each component or class of the components behaves differently and the “better” suspension for CD player is not the “best” for tube power supply. In the end that all is a huge mess where I was not able to find any rational. That is why I feel that racks are pretty much the road to nowhere.I meant the acoustic aspect of racks road to nowhere. The furniture, the continence of the racks is very nice future and shall not be discarded.
About your rack. It is nice that you have a provision to use the larger geg under the bottom of the rack. My estimate that you would need a good 8” of legs in order to use the floor as an extra shelf, of cause if you have enough crap to put in there. I do and in my world it is never too much space on the rack. You might want o look in eBay for pneumatic vibration Isolation legs. They come in set of 3 or 4 and might cost over $1000. Ironically the same legs might be listed much much chipper. Look for those that have no industrial look and work at over 80psi. It is nice if they are self-setting: you would need a compressor for it.
If I were you I would make easy extendable wings from sides of the top plates, perhaps under an angle Trust me, very soon the top shelf will be loaded with CD boxes, records, and anything ease imaginable….
THe Cat
|
|
|
Posted by N-set on
07-26-2013
|
fiogf49gjkf0d Paul, as you write the pendulum effect is unfortnately unavoidable if one wants the leveling freedome of spikes, so I try to live with that. I looked at Walker...tjaa....$1750 for a record clamp... I also saw how he works on his suspension (look at my post in the Proscenium idiocy)...disqualified! I plan to mod the spikes, but basicaly only for the looks, the pendulum is there whether you want it or not:
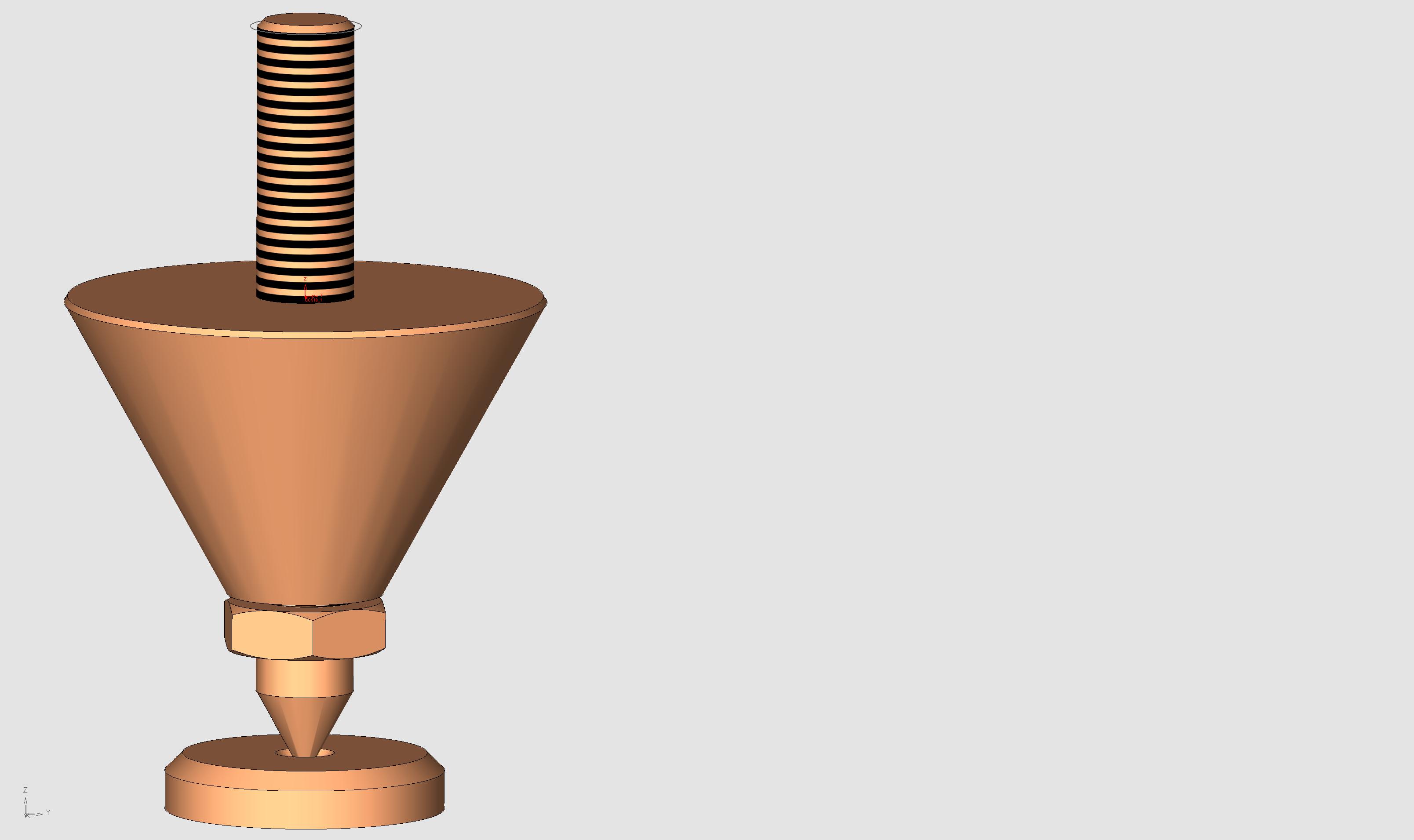
Romy, thank you for the comments.
Romy the Cat wrote: | That is why I feel that racks are pretty much the road to nowhere.I meant the acoustic aspect of racks road to nowhere. The furniture, the continence of the racks is very nice future and shall not be discarded. |
|
This is something I try to stick to. The marinated slate did add a great deal or refined, intelligent elegance to the construction. No glossy graveyard pretensions of e.g. granite (which is on top of tht poorly damped: http://www.newport.com/Granite-Optical-Structures/139776/1033/info.aspx)
Romy the Cat wrote: | You might want o look in eBay for pneumatic vibration Isolation legs. They come in set of 3 or 4 and might cost over $1000. Ironically the same legs might be listed much much chipper. Look for those that have no industrial look and work at over 80psi. It is nice if they are self-setting: you would need a compressor for it. |
|
I ws looking a lot on optical table supports, but "the real thing" is costly and I'm reluctant to buy 2nd hand. Insted I've chosen the vibraplane road and will use simple air bladders a la vibraplane:
http://search.newport.com/?x2=sku&q2=SLM-1A
It will be passive, but with time I can think of adding self-lefeling valves. It's all like a Lego.
Romy the Cat wrote: | If I were you I would make easy extendable wings from sides of the top plates, perhaps under an angle Trust me, very soon the top shelf will be loaded with CD boxes, records, and anything ease imaginable…. |
|
I very much agree, that's why I've used all the space I had between the chimneys. There will be some sort of a shelf above the rack too. Cheers, N-set
|
|
|
Posted by N-set on
07-26-2013
|
fiogf49gjkf0d Romy the Cat wrote: | I do not know if “stupid, indiscriminative mass loading is a road to nowhere”. |
|
Let me try to explain why I think so. Adding mass (e.g. sand+shot loading of steel profiles):
1) makes the vibration amplitude smaller for a given excitation energy; that's why optical tables are so heavy: they need nanometer stability; the same footfall or strong musical signal will produce much smaller vibrations with half a tone rack than with an Ikea table...unless you hit a high Q resonance; see below
2) dumps higher resonant modes (audio range), but the added mass shifts the basic, structural ULF modes lower and makes them less damped, much more difficult to filter out.
Having no experience with "listeting to the racks" as an audio activity, nor wanting to have one, I speculate that with electronics those ULF vibrations are much less of a concern (excpt maybe for big DHT's) than with TT. With TT ULF vibrations may manifest themselves as an W&F. Now, there is no one single universal damping device taking care of all the vibrations (those optical isolation legs are in fact 2-3 devices in one), and, just like with acoustic systems, damping should be viewed holistically, as a combination of different devices/material designed for different modes/frequencies. If my main TT isolation element is an air bladder with 3-5Hz fres., I don't want my rack to have it's stronegst vibrating modes in that range. This, together with shifting of fres. of the steel construction by mass loading creates a potential conflict. In my version 1, I believe the main resonant modes because of the heavy mass loading were pretty much in the 3-5Hz region. Now, in v2 with additional bracings, filled with much lighter perlite, there are somewhere higher waaay better dumped and much smaller. The main pendulum mode (the rack wobbles on the spiked points) is still at 1-2Hz and I have to live with that.
Cheers, N-set
|
|
|
|
|
Posted by Paul S on
11-24-2013
|
fiogf49gjkf0d Very cool, N-set! There is some sort of "felt" that is specifically made for bearing/sliding furniture. It is very hard - for felt - and it might be just the ticket. I would try them between your metal discs (under the spikes) and the floor, as well. Not too thick, obviously.
http://www.1877floorguy.com/hedufepa.html
I think I already pointed out to you the Walker interface discs.
https://walkeraudio.com/?product=valid-points-resonance-control-kit
Of course I would not pay their asking price, but I really like their idea, with the lead filling, etc.
Best regards, Paul
|
|
|
Posted by N-set on
11-24-2013
|
fiogf49gjkf0d Paul, thanks! But the interface I'm thinking of is between the steel frame you see in the pictures and a slate plate that will come on top of it. Something to put on top of the steel profiles, some good viscoelastic, comfortable in the constrained layer arrangement. Sorbothane is said not to be such. Not that I feel I need it badly, just thinking.
|
|
|
Posted by decoud on
11-24-2013
|
fiogf49gjkf0d What about thick, oiled, soft-tanned leather, ideally hippo? It is soft and thick, yet strong. Cowhide will do, but I have not seen it tanned quite as softly.
|
|
|
Posted by Paul S on
11-24-2013
|
fiogf49gjkf0d N-Set, to be clear, I'm suggesting you try hard felt for the frame/slate interface, as well.
Best regards, Paul
|
|
|
Posted by N-set on
11-24-2013
|
fiogf49gjkf0d Yes, I was thinking about lether too. Felt is also an option. However they both seem to me not "viscoleastic" enough and good primarly at HF, while the damped steel profile vibrates mainly at LF. I was thinking about solutions for car deadening either the old school bitumen based or moder butyl rubber, but claims are they "deaden the sound"...however one interperets that. Ideally, I'd apply a known good solution and would not have to do the typical DIY dance. At the moment I'll leave it as it is, putting the slate directly on the frame and perhaps experiment later. I'm much more interested in the performance of my monster vibraplane and a leveling roller feet idea for the electronics cage:
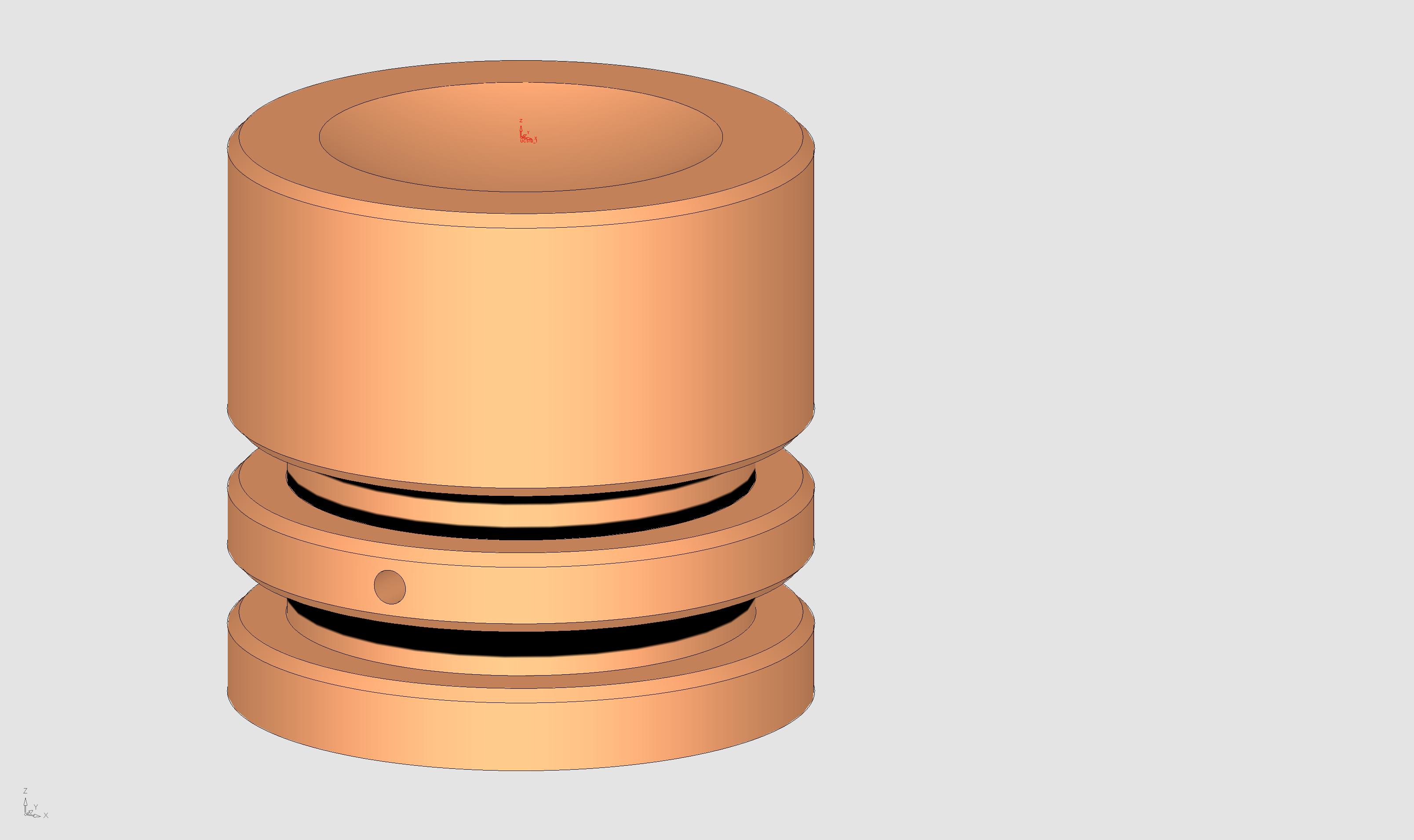
Cheers, N-set
|
|
|
Posted by Paul S on
11-24-2013
|
fiogf49gjkf0d In the real world the slate alone will not actually make continuous direct contact with the steel frame. One way or the other you will likely need something to use as "bedding" between the slate in the steel. You might look to precision machine set up for ideas, including "products" you can try. Also, it seems to me that the sort of movement this thing would be most subject to would be very low frequencies, and that might even be exacerbated by fully de-coupling the slate from the steel. While I think you can tune it effectively if you are methodical and patient, I also think it will be a try-it-and-see/hear situation, regardless.
Best regards, Paul S
|
|